Developing the Right Product
- Tim Looney
- Mar 3, 2022
- 3 min read
Updated: Mar 10, 2022
You are a medical device developer, you are $60M into development and looking to file a 510(k) with the FDA this month. The product that you have spent the last four years developing is a complex electromechanical disposable with both a therapy and diagnostic aspects. In an effort to stay on budget and time you have started to trim back your features and tailor your Indications for Use to a subset of your original goal. This is Project Management 101 where you change the deliverables to meet the schedule and budget. Little alarm bells should be going off in your head at this point because this is a slippery slope where you could destroy the market potential for the device.
The term Minimally Viable Product (MVP) is thrown around a lot, it is where you add just enough functionality and then upgrade or change it later after you establish your market share. It happens all the time but because this is medical device market, it may be worth a second thought. The concept of an MVP is great, you want to put a product out that people will use that will only contain the absolutely necessary features. Nothing more, nothing less, just what it will take to get it out on the market. Unlike other industries, medical devices are a regulated industry with approvals to ensure safety and efficacy for the patient and usability for the health care provider. Sounds great until you understand that there is a lot more to it than just adding a sensor or changing a component. There will be design work, documentation, testing, and submissions to get the change incorporated. All of these tasks will take valuable time, money, and resources. Getting in front of a frustrated or angry executive can be daunting but any change to the deliverables should be reviewed carefully. You may only get to make this decision once because these changes could take years to finalize.
Another aspect to this is that if you have released a product that could be used for another indication for use. There was a time when products were flagrantly used "off label", which means the health care provider can choose how, when, and where to use it. It was also used as a secondary or underhanded technique to get a product on the market with an easier pathway. The FDA has made great strides in curtailing this practice and requiring the proper approval for each indication for use.
What happens if you are in either of these situations? The best advice is to seek expertise to help navigate the path to market. Northeast Biomedical can provide the expertise to ensure that you are developing the right product. We are happy to work with your product to arrange an Ideation Workshop to explore ways to make and ensure that you are releasing the most appropriate product, or our engineering team can increase the product's indications for use through our ISO 13485 certified development process.
Northeast Biomedical is a medical device product development and contract manufacturing company that works with companies at all stages of development. Our development process is ISO 13485:2016 certified. We have the ability to augment your efforts with our expertise to help you get your projects to the next stage in an efficient and timely manner.
We offer product development services including:
Electromechanical Instrumentation Design & Development
Product Development Services
Disposable Design & Development
Low Volume Contract Manufacturing
Ideation Workshop
Engineer on Call Service
We have a team of highly skilled engineers who specialize in the design and development of medical products and equipment. We have worked on a variety of projects in the medical technology space including catheters, disposable devices, sensors, ultrasound integration, optical fiber and laser products, instrumentation, surgical tools, point of care products, podiatry devices, test fixtures, surgical robots, machine vision, and automation equipment. Our website has information about us and on our approach to projects. www.northeastbiomed.com
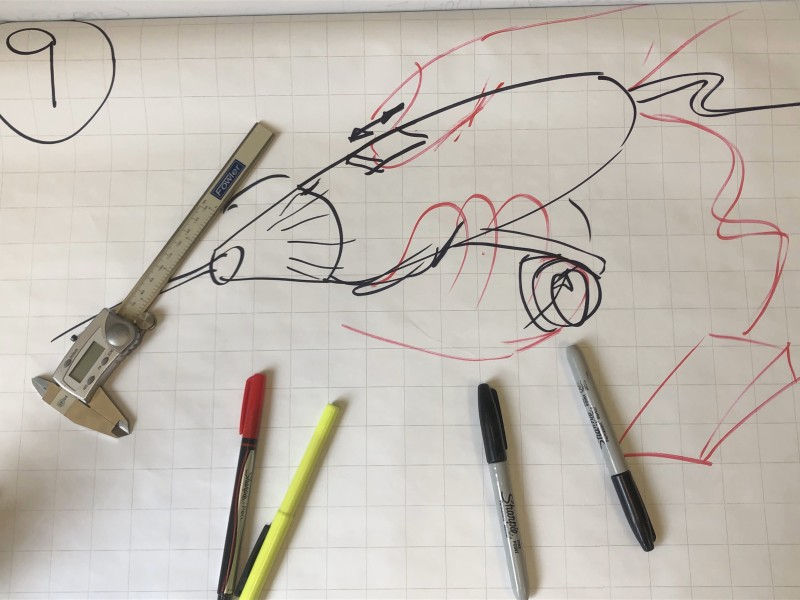
Comments